Khử chọn lọc xúc tác – Selective Catalytic Reduction (SCR) là một công nghệ kiểm soát khí thải quan trọng được sử dụng ở nhiều nhà máy điện chạy bằng than, sinh khối, chất thải thành năng lượng và khí đốt. Nhiều hạng mục phải được xem xét khi thiết kế hệ thống SCR để tối ưu hóa hiệu suất.
Nếu không có hệ thống kiểm soát khí thải phù hợp, một lượng đáng kể NOx trong không khí có thể được thải ra từ quá trình đốt nhiên liệu tại các nhà máy điện. NOx bao gồm nitơ oxit (NO), nitơ đioxit(NO2) và các oxit nitơ khác. Có một số tác động tiêu cực đến môi trường khi thải quá nhiều NOx vào khí quyển. Phòng thí nghiệm Công nghệ Năng lượng Quốc gia (NETL) của Hoa Kỳ thống kê như sau:
- NOx là thành phần chính trong việc hình thành ôzôn trên mặt đất, gây ra các vấn đề nghiêm trọng về hô hấp.
- Các vấn đề về hô hấp có thể xảy ra do bản thân việc tiếp xúc với NO2 , nhưng điều đáng lo ngại là NOx phản ứng tạo thành các hạt nitrat trong không khí hoặc sol khí axit, có tác dụng tương tự.
- Cùng với các oxit lưu huỳnh (SOx), NOx góp phần hình thành mưa axit và gây ra nhiều vấn đề về môi trường.
- NOx có thể làm suy giảm chất lượng nước do nước có quá nhiều chất dinh dưỡng, gây ra tình trạng dư thừa tảo.
- Các hạt chứa nitơ trong không khí làm giảm tầm nhìn.
- NOx có thể phản ứng tạo thành đinitơ oxit (N2O), là một loại khí nhà kính và góp phần làm trái đất nóng lên.
1. Khử chọn lọc xúc tác (SCR)
Hệ thống khử chọn lọc xúc tác (SCR) loại bỏ NOx khỏi khí thải phát ra từ lò hơi của nhà máy điện, tua bin khí và các nguồn đốt khác. Hệ thống SCR làm giảm có chọn lọc lượng phát thải NOx bằng cách bơm amoniac (NH3) vào khí thải phía trước chất xúc tác. NOx phản ứng với NH3 và oxy (O2) để tạo thành nitơ (N2) và nước (H2O), chủ yếu theo các phương trình sau:
4NH3 + 4NO + O2 ➝ 4N2 + 6H2O
2NH3 + NO + NO2 ➝ 2N2 + 3H2O
4NH3 + 2NO2 + O2 ➝ 3N2 + 6H2O
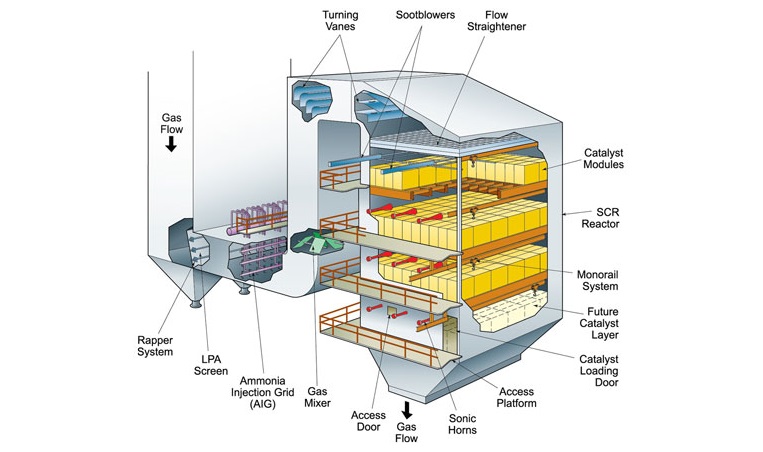
Sơ đồ hệ thống SCR
Bề mặt hoạt động của chất xúc tác thường là kim loại quý, oxit kim loại cơ bản (titan hoặc vanadi) hoặc vật liệu gốc zeolit. Theo NETL, chất xúc tác gốc kim loại thường được sử dụng làm lớp phủ trên bề mặt kim loại hoặc gốm, trong khi chất xúc tác zeolite thường là vật liệu đồng nhất tạo thành cả bề mặt hoạt động và chất nền.
Cấu hình hình học của thân xúc tác được thiết kế để có diện tích bề mặt tối đa và giảm thiểu sự cản trở đường dẫn khí thải để tối đa hóa hiệu suất chuyển đổi và giảm thiểu áp suất ngược lên tuabin. Cấu hình phổ biến nhất là thiết kế tấm nguyên khối và dạng tổ ong.
Một yếu tố quan trọng ảnh hưởng đến hiệu suất của SCR là nhiệt độ hoạt động. Chất xúc tác kim loại cơ bản có nhiệt độ vận hành cho các ứng dụng nhiên liệu sạch khoảng 400 oF đến 800 oF (khoảng 200 oC đến 425 oC). Phạm vi trên của nhiệt độ này có thể được tăng lên bằng cách sử dụng chất xúc tác zeolite lên tối đa 1100oF (khoảng 600 oC). Do phạm vi nhiệt độ hoạt động cần thiết cho chất xúc tác SCR thông thường (600oF đến 750oF), việc tích hợp vào máy tạo hơi thu hồi nhiệt (HRSG) thường yêu cầu tách phần thiết bị bay hơi (hoặc nồi hơi) áp suất cao (HP) để chứa lớp xúc tác SCR và thiết bị phun amoniac.
2. Khử chọn lọc không xúc tác (Selective non-catalytic reduction – SNCR)
Khử chọn lọc không xúc tác (SNCR) là một công nghệ kiểm soát khí thải sau đốt khác để giảm NOx. SNCR hoạt động bằng cách bơm thuốc thử gốc amoniac vào lò ở một vị trí được xác định chính xác. Công nghệ này hấp dẫn vì nó đòi hỏi chi phí vốn tương đối thấp để lắp đặt.
Nguyên lý hệ thống SNCR
Theo Cơ quan Bảo vệ Môi trường Hoa Kỳ (EPA), hơn một nửa số lò hơi tiện ích có SNCR tương đối nhỏ (200 MW trở xuống), nhưng khoảng 24% lớn hơn 300 MW. Hơn 70% lò hơi tiện ích sử dụng SNCR đốt than làm nhiên liệu chính và hầu hết các lò hơi khác đốt sinh khối. SNCR có thể được áp dụng dưới dạng bộ điều khiển NOx độc lập hoặc với các công nghệ khác như bộ điều khiển quá trình đốt cháy. Hệ thống SNCR cũng có thể được thiết kế để vận hành theo mùa trong một số trường hợp, thay vì vận hành quanh năm.
“SNCR thường hoạt động ở nhiệt độ từ 900 oC đến 1000 oC. Tương tự như SCR, các oxit nitơ được khử thành nitơ bằng cách bơm amoniac hoặc urê. Việc điều chỉnh nhiệt độ chính xác sẽ xác định hiệu quả của SNCR, cũng như các tác dụng phụ không mong muốn như amoniac rò rỉ”. Carsten Walddörfer, trưởng nhóm Nghiên cứu và Phát triển (R&D), Hệ thống Công nghệ Sạch Quản lý Sản phẩm của Dürr Systems AG giải thích.
“Tùy thuộc vào điều kiện quy trình, bộ SNCR được lắp đặt trực tiếp trong buồng đốt hoặc ở phần đầu tiên của lò hơi nhiệt thải. Câu hỏi về chất khử thường được lựa chọn tùy thuộc vào quy mô nhà máy. Thông thường, các tổ máy có quy mô nhỏ hơn được vận hành bằng dung dịch urê, các tổ máy có quy mô lớn hơn được vận hành bằng nước amoniac”, Walddörfer cho biết.
Việc lựa chọn giữa hệ thống SCR và SNCR gần như hoàn toàn dựa trên tỷ lệ phần trăm loại bỏ khí thải cần thiết. Ryan Hensel, giám đốc đề xuất cấp cao và chuyên gia về chủ đề SCR tại Babcock & Wilcox (B&W), cho biết: “SCR và SNCR khác nhau đáng kể về khả năng của chúng”. Hensel cho biết SCR thường được sử dụng trong các ứng dụng đốt than, sinh khối, khí tự nhiên và biến chất thải thành năng lượng. “Chúng tôi đã cho thấy khả năng loại bỏ hơn 90% đối với tất cả các ứng dụng đó. Trên SNCR của nồi hơi quy mô tiện ích, bạn có thể đang xem xét ở đâu đó nhiều hơn trong phạm vi 30% đến 40%,” ông nói.
Tuy nhiên, có một số ứng dụng trong đó SNCR có thể đạt được tỷ lệ loại bỏ cao hơn. Hensel cho biết: “Trong một số ứng dụng công nghiệp, nơi chúng ở trong phạm vi nhiệt độ có thể chấp nhận được lâu hơn, chúng tôi đã đạt được mức loại bỏ trong khoảng 60% đến 70%, nhưng một lần nữa, đó là tập hợp các điều kiện tuyệt đối phù hợp”.
3. Chất xúc tác SCR
Dan Johnson, phó chủ tịch phát triển kinh doanh của CORMETECH, giải thích rằng có ba yếu tố có thể được điều chỉnh để tạo ra chất xúc tác tối ưu cho bất kỳ ứng dụng SCR cụ thể nào. “Một trong số đó là bề mặt đệm,” ông nói. “Bề mặt đệm là kích thước của các lỗ bề mặt cho phép khí đi qua chất xúc tác. Nếu khí có bất kỳ loại hạt nào trong đó, chẳng hạn như tro than, bạn cần phải có hình dạng của chất xúc tác sao cho nó có thể vượt qua hạt đó.”
Johnson cho biết không có gì lạ khi có các khe hở 7 mm trên các đơn vị than để giải quyết vấn đề về tro. CORMETECH cũng có các chất xúc tác được chế tạo đặc biệt cho môi trường có hàm lượng tro cao, nơi mà lỗ hở của tế bào thậm chí còn lớn hơn nhưng vẫn duy trì diện tích bề mặt xúc tác cực cao. Tuy nhiên, trong một thiết bị chu trình hỗn hợp đốt bằng khí, các khe hở của ngăn thường nhỏ hơn nhiều thấp ở mức 1.2 mm, 1.4 mm hoặc 2.1 mm. Ông nói: “Và có tất cả mọi thứ ở giữa, vì vậy điều thực sự quan trọng là chọn kích thước bước phù hợp cho hạt mà bạn có thể nhìn thấy trong khí thải của mình”.
Mục thứ hai phải được xem xét là công thức xúc tác. “Trên một đơn vị than, các công thức rất khác nhau giữa các đơn vị, bởi vì bạn đang cố gắng cân bằng một số thứ. Bạn đang thêm kim loại xúc tác vào chất xúc tác để có hoạt tính khử NOx, nhưng khi bạn thêm nhiều kim loại xúc tác hơn, nó có thể oxy hóa nhiều SO2 thành SO3 hơn, vì vậy bạn đang thiết kế chất xúc tác dành riêng cho một đơn vị cụ thể để tối đa hóa hoạt động của chất xúc tác liên quan đến quá trình khử NOx, đồng thời giảm thiểu hoạt động của chất xúc tác liên quan đến quá trình oxy hóa SO2” Johnson giải thích.
Các đơn vị khí đã thiết lập các công thức thường được sử dụng. Johnson cho biết : “Những công thức đó thay đổi, không phải với quá trình oxy hóa SO2 thay đổi mà ở nhiệt độ khác nhau”. “Khi nhiệt độ tăng cao hơn, bạn phải thay đổi hỗn hợp kim loại xúc tác mà bạn đang sử dụng vì một số trong số chúng sẽ không hoạt động tốt ở nhiệt độ cao hơn. Tại CORMETECH, chúng tôi tự hào về kỹ thuật tùy chỉnh các chất xúc tác của mình cho mọi ứng dụng và điều đó thực sự cần thiết để đáp ứng các yêu cầu về hiệu suất.”
Việc cân nhắc cuối cùng là thiết kế mô-đun – cấu trúc bao quanh chất xúc tác. “Mọi chất xúc tác đều được đóng gói hoặc đặt bên trong khung thép. Sau đó, khung đó được lắp vào thiết bị và có thể có rất nhiều khung – chẳng hạn như có thể có 140 khung trong một lớp trong một đơn vị than,” Johnson nói. Việc thay đổi thiết kế mô-đun tiêu chuẩn thường dựa trên các biến số dòng khí (dọc so với ngang) và/hoặc mức giảm áp suất mong muốn. Thiết kế mô-đun sẽ thay đổi dựa trên mục tiêu hiệu suất và để phù hợp về mặt cơ học bên trong thiết bị.
Chất xúc tác SCR bề mặt cực cao của CORMETECH
4. Nhiệt độ là một biến quan trọng
Như đã đề cập trước đó, nhiệt độ vận hành ảnh hưởng đến hiệu suất của hệ thống SCR. “SCR thường hoạt động trong phạm vi nhiệt độ từ 300 oC đến 350o C (572oF đến 662oF). Tùy thuộc vào thành phần khí thải, nhiệt độ thấp hơn có thể được áp dụng”, Walddörfer của Dürr Systems cho biết. “Ví dụ, nếu khí thải đi vào hệ thống không ở nhiệt độ yêu cầu, thì nó phải được làm nóng trước bằng cách sử dụng bộ trao đổi nhiệt không khí. Sau đó, không khí được làm nóng thêm bằng đầu đốt hoặc loại lò sưởi khác cho đến khi đạt đến nhiệt độ vận hành chất xúc tác. Trong một số thông số kỹ thuật, bộ SCR có thể được tích hợp trực tiếp vào hệ thống thu hồi nhiệt thải ở giữa nồi hơi và bộ tiết kiệm”.
Hensel của B&W cho biết: “SCR là một loại quy trình tối ưu hóa trên nhiều thứ. “Phản ứng xúc tác phụ thuộc rất nhiều vào nhiệt độ. Vì vậy, một khi bạn đặt nhiệt độ thiết kế, nếu bạn tăng cao hơn hoặc thấp hơn một chút, điều đó sẽ có tác động nhất định đến hiệu suất của chất xúc tác.”
Trong trường hợp của một số nhà máy điện chạy bằng than và khí đốt, điều đó có thể là một vấn đề hiện nay. Khi ngày càng có nhiều năng lượng gió và năng lượng mặt trời được bổ sung vào lưới điện, các yêu cầu vận hành tại nhiều nhà máy đã thay đổi. “Khi các thiết bị không còn tải cơ bản và xem xét tải một phần nhiều hơn hoặc duy trì tải một phần lâu hơn, sẽ có một số hậu quả đi kèm với điều đó. Về mặt khí, mọi việc dễ dàng hơn một chút, vì khí tự nhiên không có lưu huỳnh trong khí, không có hạt trong dòng khí, nó thực sự chỉ tạo ra một chút biến đổi trong hiệu suất của chất xúc tác” Hensel giải thích.
Ông nói: “Có thể nếu lúc đó bạn biết những gì bạn biết bây giờ thì bạn đã chọn một nhiệt độ khác để tối ưu hóa, nhưng thông thường theo kinh nghiệm của chúng tôi, đó là tác động tương đối nhỏ đến tỷ lệ loại bỏ. Trường hợp có thể gặp vấn đề hơn là một số ứng dụng có hạt hoặc lưu huỳnh trong khí thải”.
“Về hạt, nếu chúng ta thiết kế mọi thứ để giữ cho tất cả các hạt đó bị cuốn theo nhắm vào các khu vực bụi phóng xạ cụ thể trong hệ thống nơi chúng ta có thể nắm bắt được nó và sau đó, chẳng hạn, chúng ta đang chạy với một nửa vận tốc đó, điều đó có thể thay đổi một số những lĩnh vực mà chúng tôi đã nhắm mục tiêu cụ thể trước đây”, Hensel cho biết.
“Trên lưu huỳnh, ở nhiệt độ thấp hơn, amoniac có thể phản ứng với SO3 trong khí thải để tạo thành amoni bisulfate. Đó là một chất dính sẽ làm tắc nghẽn chất xúc tác của bạn và có thể gây ra các vấn đề thực sự về hiệu suất của chất xúc tác trong thời gian ngắn. Vì vậy, nếu một thiết bị đang chạy ở mức tải 30% và được thiết kế để đạt 100%, bạn chỉ cần lưu ý duy trì ở nhiệt độ vận hành ở mức mà bạn không thấy hiện tượng đó xảy ra”, Hensel nói.
Một số phương án trang bị thêm có thể áp dụng để giảm thiểu các vấn đề liên quan đến việc thay đổi điều kiện vận hành bao gồm sửa đổi thiết bị làm sạch chất xúc tác. “Nếu các điều kiện vận hành của thiết bị dẫn đến sự tích tụ tro tập trung hơn, thường là dọc theo bức tường phía trước của lò phản ứng SCR, nếu thiết bị hoạt động ở mức tải thấp hơn trong thời gian dài, thì chúng tôi đã chuyển sang các thiết bị và trang bị thêm máy thổi bồ hóng hoặc nâng cấp lên loại mạnh hơn những gì chúng tôi đã lắp đặt ban đầu để nhắm mục tiêu vào các khu vực cụ thể trong lò phản ứng,” Hensel lưu ý.
Nguồn: tổng hợp
Chugai Technos là đơn vị đã thực hiện kiểm tra hiệu suất hệ thống SCR và hiệu chỉnh hệ thống phun amoniac (AIG) cho rất nhiều nhà máy nhiệt điện tại Việt Nam (NMNĐ Formosa Đồng Nai, Mông Dương 2, Vĩnh Tân 2, Duyên Hải 1, Vũng Áng 1).
Nếu Quý khách hàng có nhu cầu kiểm tra xác nhận lại hiệu suất của hệ thống SCR và hiệu chỉnh AIG, hãy gọi ngay đến Hotline: 0909-714-566 hoặc để lại thông tin TẠI ĐÂY để Chugai Technos nhanh chóng liên hệ để giải đáp các thắc mắc và hỗ trợ.